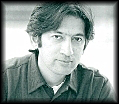
Editor's Ramblings
Relentless Pursuit: Fatigue Ensues
by
Naeem Ismat (Guest Contributor)
|
Sept., 2018
When new lean teams gather for the first time there is usually an imperative for the program. From operations managers, maintenance managers, quality control manager to C-level participants and plant floor workers, there is an initial enthusiasm for the concept and quasi-religious fervor of eliminating waste and zealous appreciation that this is the beginning of a long road to continuous process improvement.
Fast forward two years later and those same folks, if still employed by the same company, are tired, far less enthusiastic, and even bored with the lean process.
Lean manufacturing does work. Thousands of examples of streamlining, eliminating redundancy and waste fill the search criteria of Google. More than any single factor, when the management leadership that advocated lean at the start, loses enthusiasm, it permeates those on the lean initiative team and company-wide. Just as there are term limits in politics, it is vital that lean teams have different leaders who can infuse life into tired lean programs.
Transitioning lean leadership must be part of the plan from the start. Too often the first projects are the "low hanging fruit" or obvious areas of improving the manufacturing organization that are sorely in need of improvement. After six months to a year, the projects that yielded fantastic cost-savings and better processes, are replaced with seemingly mundane and less interesting areas of improvement. Ironically by shifting the lean leadership, a totally different perspective can revive life into a lean initiative team.
A quality control manager's perspective, for example, is quite different than a plant manager's perspective or a human resources manager's perspective. By shifting the different roles within the organization into the lean initiative team leadership, empathy, compassion, and refreshing the zeitgeist of the entire team can happen. It is not by accident. Everyone on the lean team must know their leadership turn will happen. Rarely is someone in maintenance asked to consider the hiring practices of the organization, yet it is precisely this notion of "walking in someone else's shoes" that creates a kind of kaizen event. All these different points of views, agendas, ideas, and experiences are precisely the backbone and quintessential value in lean manufacturing. Through the linear functionality of one's own job, the organization suffers. Only when the industrial operation is viewed as a whole, from a wide variety of vantage points, can lean manufacturing remain interesting, fun, and truly continuous.
Long international flights have multiple pilots to avoid the fatigue one pilot might experience during flight. When lean teams are getting tired, allow team members a break; infuse the team with a new member and new point of view. Running a marathon is akin to running a manufacturing company; it is not a 5K or 10K race. Lean is for the long haul and strategies to keep going and growing through wasteful practices requires discipline, rigor, and planning. Lean road kill is simply not an option. Dig deep and set a series of finish lines to keep lean alive.