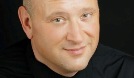
Electronic Kanban for Faster Turns, Reduced Inventory Improves Top Supplier in Commercial Trucking
by Thomas R. Cutler | April, 2009
Manufacturing Insights
Automation, Control & Plant Intelligence - Articles, Analysis, Reviews, Interviews & Views
by Thomas R. Cutler | April, 2009
Manufacturing Insights
YOU MAY LIKE:
Popular Articles
Manufacturing Insights