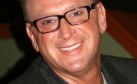
Too Many Metrics Demand-Driven Manufacturing Metrics for Action
by Thomas R. Cutler | August 10, 2016
Automation, Control & Plant Intelligence - Articles, Analysis, Reviews, Interviews & Views
by Thomas R. Cutler | August 10, 2016
YOU MAY LIKE:
Popular Articles
Manufacturing Insights