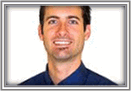
Automation, Control & Plant Intelligence - Articles, Analysis, Reviews, Interviews & Views
YOU MAY LIKE:
Popular Articles
Manufacturing Insights