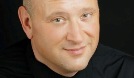
Overall Equipment Efficiency from 65% to 75% Shown at Pollak-APD
by Thomas R. Cutler | May, 2008
Manufacturing Insights
Automation, Control & Plant Intelligence - Articles, Analysis, Reviews, Interviews & Views
by Thomas R. Cutler | May, 2008
Manufacturing Insights
YOU MAY LIKE:
Popular Articles
Manufacturing Insights