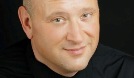
Lean Warehouse Control Systems Transform Distribution Centers
by Thomas R. Cutler | December, 2006
Manufacturing Insights
Automation, Control & Plant Intelligence - Articles, Analysis, Reviews, Interviews & Views
by Thomas R. Cutler | December, 2006
Manufacturing Insights
YOU MAY LIKE:
Popular Articles
Manufacturing Insights