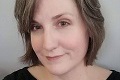
Upgrade to Industry 4.0 While Running A Legacy System
by Marla Keene | November, 2019
Energy | Internet of Things | Manufacturing | Sensors
Automation, Control & Plant Intelligence - Articles, Analysis, Reviews, Interviews & Views
by Marla Keene | November, 2019
Energy | Internet of Things | Manufacturing | Sensors
YOU MAY LIKE:
Popular Articles
Manufacturing Insights