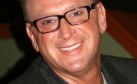
The Changing Requirements of Labor in U.S. Manufacturing
by Thomas R. Cutler | November, 2011
Manufacturing Insights
Automation, Control & Plant Intelligence - Articles, Analysis, Reviews, Interviews & Views
by Thomas R. Cutler | November, 2011
Manufacturing Insights
YOU MAY LIKE:
Popular Articles
Manufacturing Insights