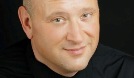
Simultaneous Improvement: Safety and Productivity
by Thomas R. Cutler | February, 2009
Manufacturing Insights
Automation, Control & Plant Intelligence - Articles, Analysis, Reviews, Interviews & Views
by Thomas R. Cutler | February, 2009
Manufacturing Insights
YOU MAY LIKE:
Popular Articles
Manufacturing Insights