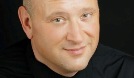
Two Years Later: A Look at the Demand Driven Supply Chain Technology
by Thomas R. Cutler | April, 2008
Manufacturing Insights
Automation, Control & Plant Intelligence - Articles, Analysis, Reviews, Interviews & Views
YOU MAY LIKE:
Popular Articles
Manufacturing Insights