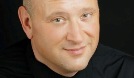
Lean Automation Optimization Found in the Mobile Warehouse
by Thomas R. Cutler | November, 2007
Manufacturing Insights
Automation, Control & Plant Intelligence - Articles, Analysis, Reviews, Interviews & Views
by Thomas R. Cutler | November, 2007
Manufacturing Insights
YOU MAY LIKE:
Popular Articles
Manufacturing Insights