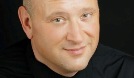
Moving from “Just in Case” to Just-in-Time
by Thomas R. Cutler | November, 2006
Manufacturing Insights
Automation, Control & Plant Intelligence - Articles, Analysis, Reviews, Interviews & Views
by Thomas R. Cutler | November, 2006
Manufacturing Insights
YOU MAY LIKE:
Popular Articles
Manufacturing Insights