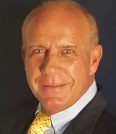
The Problem: ERP Supplier Portal Designed Around MRP Forecast Management The Solution: Demand Driven Enterprise-wide Supply Chain Solutions
by Frank Kapper | Dec 17, 2017
Automation, Control & Plant Intelligence - Articles, Analysis, Reviews, Interviews & Views
by Frank Kapper | Dec 17, 2017
YOU MAY LIKE:
Popular Articles
Manufacturing Insights