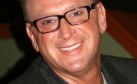
Automation for Retailer Expands Rapidly in 2013
by Thomas R. Cutler | January, 2013
Manufacturing Insights
Automation, Control & Plant Intelligence - Articles, Analysis, Reviews, Interviews & Views
by Thomas R. Cutler | January, 2013
Manufacturing Insights
YOU MAY LIKE:
Popular Articles
Manufacturing Insights